Over the past year and a half, several states, including New York, Massachusetts, and Illinois, have adopted the measures of the 2018 International Energy Conservation Code (IECC) for buildings in certain sectors. AN asked leading manufacturers and architects to describe what insulating and solar- factor performance benchmarks the code requires of glass in building facades. Below, they identify how it may be difficult to meet those requirements and adapt for a more energy-efficient future.
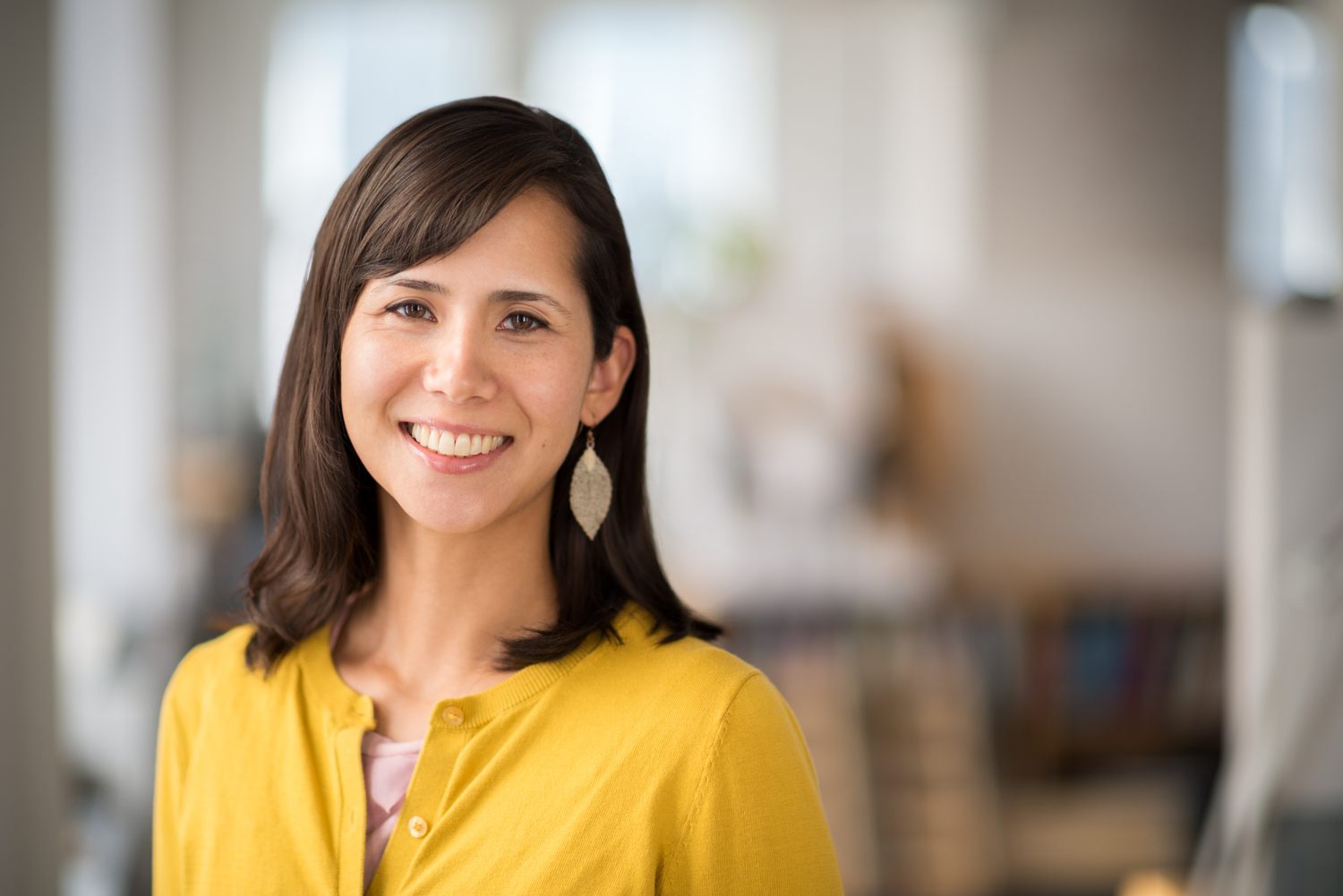
Patricia Culley
Associate Principal, Bohlin Cywinski Jackson
A holistic, integrated design strategy to achieve energy efficiency is often the best method to meet energy code requirements while providing design flexibility. In the 2018 IECC, the prescriptive pathway and ASHRAE 90.1-2016 outline specific requirements for glazing assemblies. However, the performance pathway allows designers to measure glazing assembly performance in relation to the opaque portions of the building envelope; this allows designers more creativity to meet performance requirements while satisfying design aesthetics. Energy requirements vary by climatic zone. In most of the country (generally zones 3 through 6), window assemblies meeting 2018 IECC will likely require Low-E, gas-filled double glazing within thermally broken frames with warm edge spacers. In colder areas, like climate zone 8, triple glazing may be necessary, though it is more challenging to source at this time.
Recognizing the importance of energy conservation, codes will likely continue to become more stringent in the future, and manufacturers will need to continue to advance product performance capabilities. From a design perspective, it is the hope that new advances in thermal improvements of glazing framing systems, glazing coatings, suspended films, and captured gases will achieve better energy performance, while maintaining high levels of transparency and neutral color. Glass facades may become more sophisticated with passive and active technology improvements, advancements in materials, and fabrication technologies, and achieve better performance and cost-efficiency with an integrated approach. Glazing system improvements may incorporate both active and passive technologies, advanced materials such as engineered composite materials, phase-change materials, and nanotechnology.
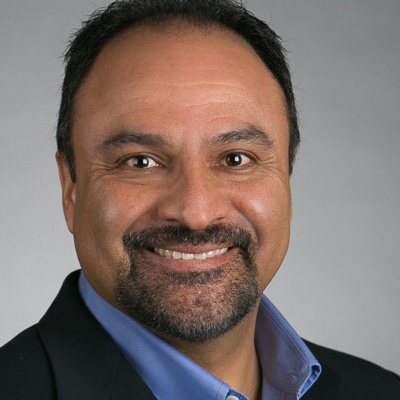
Ivan Zuniga
Product Manager, Kawneer
Over the last several years, Kawneer has been designing systems using advanced thermal break technology such as dual pour and debridge systems, larger thermal breaks using polyamide material, and the introduction of our patented IsoPour Thermal Break. We have begun documenting higher performing glass (warm edge spacers) in insulating glass units, which architects can use in their thermal performance calculations. To go along with this, our Solector Sun Shading Estimator tool is available on our website to help architects select the right products for meeting thermal and solar performance requirements. Several products have been explicitly designed for both standard double-pane insulating glass unit and triple-pane insulating glass unit capabilities. And we are working more closely than ever with consultants on air barrier connections to help provide more energy-efficient building solutions.
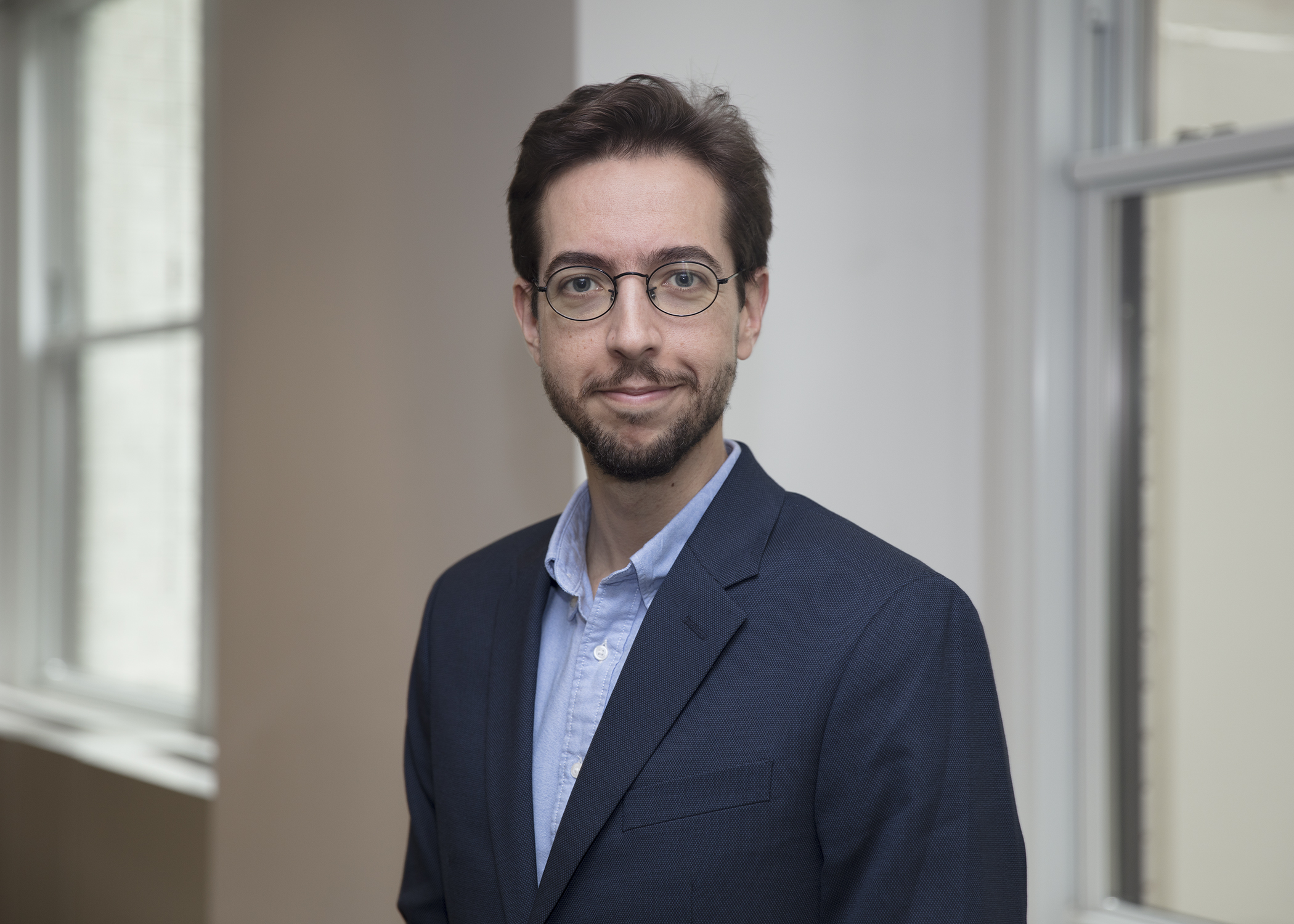
Carlos Cerezo Davila
Sustainable Design Leader & Senior Associate Principal, Kohn Pedersen Fox
The increased targets for overall thermal performance that we are facing in our ongoing projects in Boston and New York are high enough to require the envelope to perform on its own. Responding to the challenge has been very exciting for us, as it has allowed for a more nuanced conversation about facade design with clients, developers, and brokers. In several projects, this has led to a reassessment of glazing ratios to avoid more expensive triple glazing solutions, resulting in facade designs that incorporate more opacity. This creates new opportunities to focus on materiality, detail, and craft—opportunities that are somewhat limited in standardized commercial curtain wall systems—and to rethink unitized construction delivery systems. At the same time, we are relying more on thermal and energy modeling tools to closely coordinate glazing throughout the building to enable the use of smarter heating and cooling systems.
Looking forward, it is also clear that these new codes, combined with new city-specific regulations to encourage net zero–carbon buildings, are opening the door to more advanced glazing technologies that were quickly dismissed before, given their cost. In colder climates, triple glazing has become a more mainstream commercial solution, and dynamic electrochromic glazing, considered a rare technology ten years ago, is being requested by our clients today. With even more advanced solutions like vacuum insulated glazing on the horizon, we expect to see exciting changes moving forward.

David Duly
Senior Engineer, Pilkington North America
In order to decrease the U-value of insulated glass units (IGUs), the use of a solar control tinted glass product as the outboard glass layer together with a Low-E coated glass with the coating along the #3 surface may be specified. Additional performance may be achieved by specifying a solar control tinted Low-E glass with the coating along the #2 surface and an additional Low-E coated glass with the coating along the #3 surface. The next step is the so-called #4 surface low-e, where the solar control tinted Low-E glass with the coating along the #2 surface and an additional Low-E coated glass with the coating along the #4 surface are selected. This combination will result in a reduction in the U-value compared with the case where the Low-E coated glass is placed on the #3 surface.
Vacuum insulating glass may be selected for existing window replacement projects where a narrow profile and a lower U-value are specified. This glazing type reduces the heat transfer modes of conduction and convection because of the creation of a vacuum within the narrow airspace (approximately 0.2 millimeters thick) of the IGU.
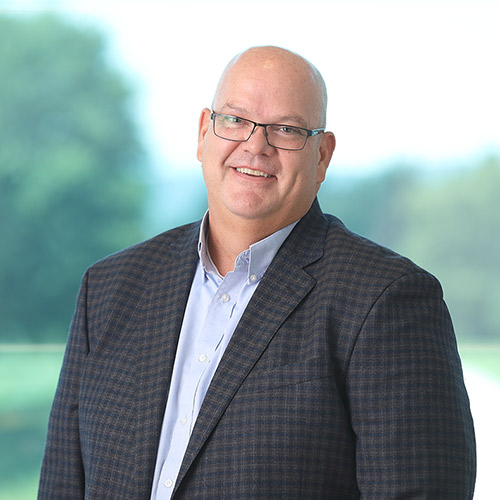
Lucas Hamilton
Manager of Building Science Applications, Saint-Gobain North America & CertainTeed
We know that views of the outside world are both aesthetically pleasing and beneficial to occupant well-being. We’ve also learned that it’s easier to give people access to nature than it is to re-create it. Unfortunately, the windows that provide this access are traditionally one of the lowest-performing parts of a building when it comes to energy efficiency. This has limited our window-to-wall ratio for some time now, but that is finally changing. Energy-efficient features such as dynamic electrochromic glazing integrated with smart automatic lighting produce significant energy savings and lower operational costs of mechanical systems, all while providing uninterrupted views of nature.
It’s not impossible to meet energy goals while creating better spaces for people, but we have to build differently than we have in the past. It begins with an understanding that the long-term, compound financial, physical, and environmental paybacks that will be achieved over the installation’s life cycle outweigh the initial investment in the systems that afford them.
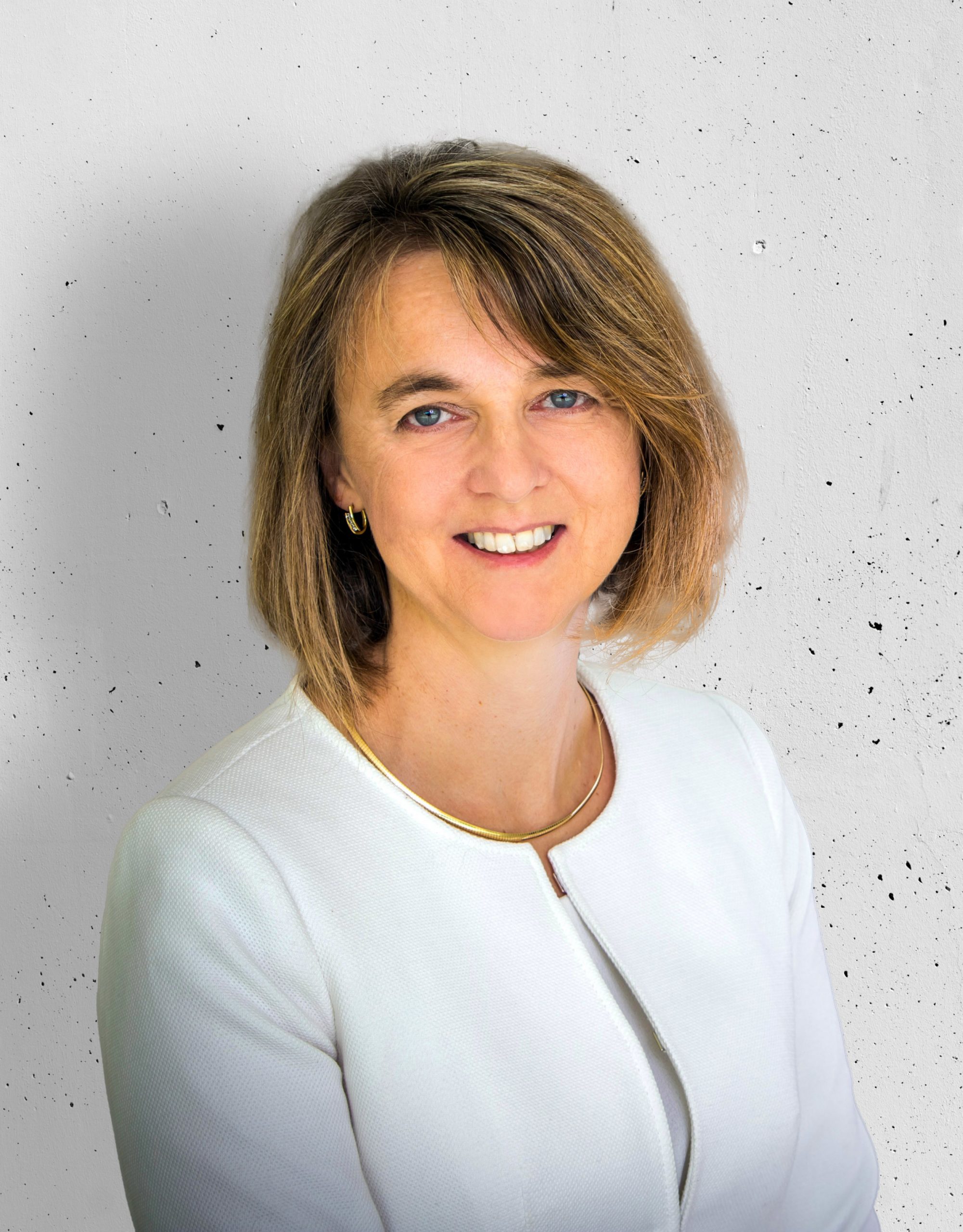
Helen Sanders
General Manager, Technoform Glass Insulation North America
The prescriptive U-factors for fenestration in the 2018 IECC are the same as those in the 2015 IECC, so the new code will make no difference for those following the prescriptive compliance path. However, buildings with higher window area than the prescriptive path allows, prescriptive requirements for the other systems in the building have likely tightened up. The biggest change for architects is not necessarily in the adoption of the 2018 IECC, but the additional requirements that local jurisdictions have established. For example, Massachusetts and New York City have enacted the use of envelope backstops or minimum requirements for performance that a building envelope should meet.
Trading off better internal systems for poorer envelope performance is not so easy when the baseline internal system performance has been increased, and it is especially difficult where stringent envelope backstops are in place. It also becomes more difficult to get to higher glazed transparent areas because the performance comparison is the prescriptive window area of 30 percent or 40 percent if lighting controls are used in more areas.
When higher glazed areas are desired, U-factors lower than the prescriptive path requirements are needed. Because of these backstops, architects likely have to make significant changes to their go-to facade system designs. They are hungry for more information on how to specify the appropriate fenestration products that exceed the current 2018 IECC prescriptive path requirements of 0.38 Btu/ oF.hr.ft2 for climate zones 4 (New York City) and 5 (Boston, Chicago). There are many curtain wall and fixed window systems that meet a U-factor of 0.38 Btu/oF.hr.ft2. For a captured curtain wall, exceeding those standards typically requires a minimally thermally broken aluminum frame, dual-pane Low-E coated insulating glass with argon, and a warm edge spacer. Improving the thermal break performance of the frame can reduce the reliance on strategies such as the use of argon to improve the performance of the glass package. Structurally glazed curtain wall systems can typically achieve even lower U-factors than their equivalent captured systems with the same glazing infill because the thermal bridging from outside to inside is reduced.
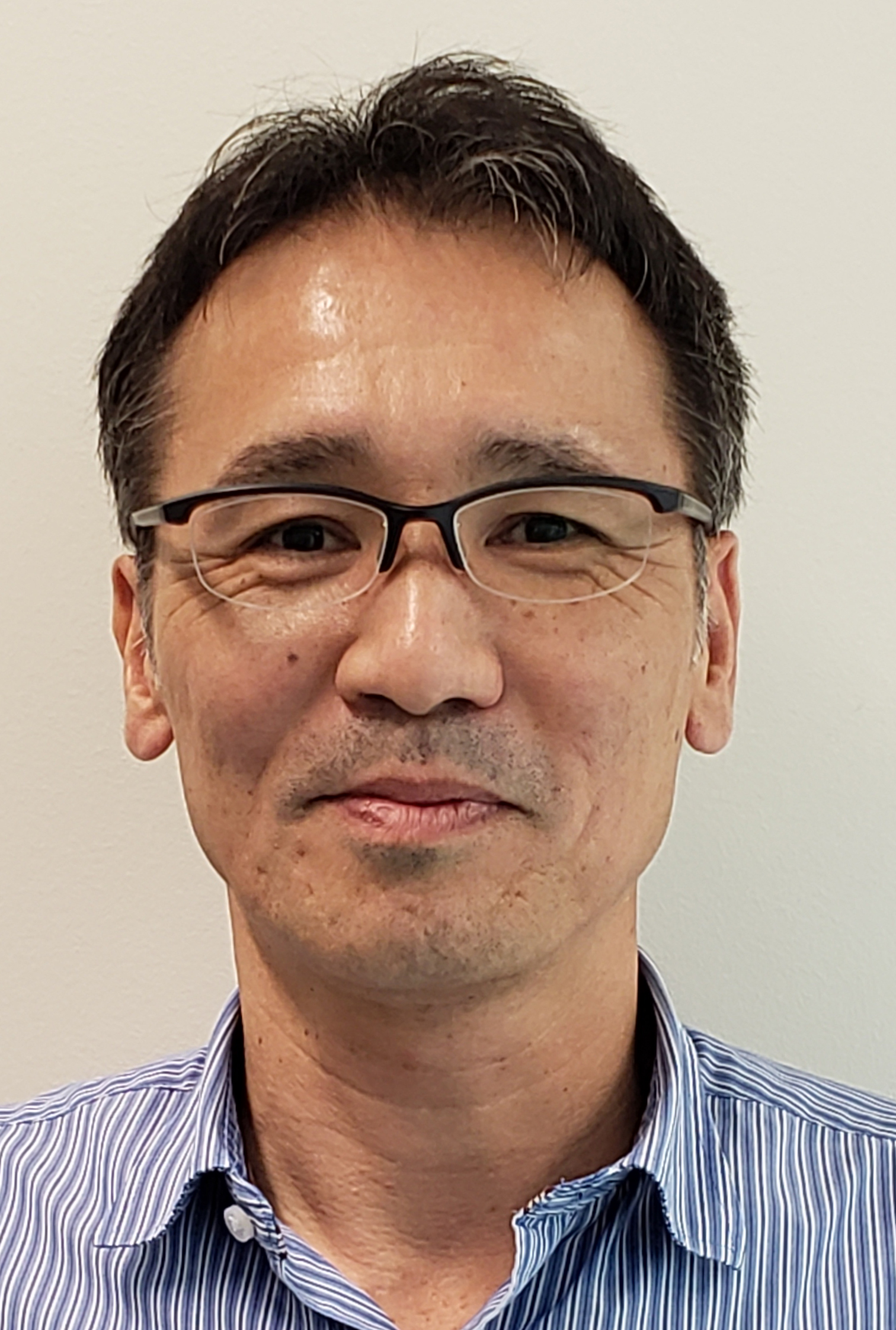
Mick Moriya
Director of Product Development, YKK AP America
While there are multiple avenues to achieve a higher level of energy efficiency, framing should be highly considered to meet and exceed energy codes. Advanced glazing solutions, such as Low-E glass or argon-filled glass, work to improve the center-of-glass thermal performance value. However, a system’s thermal performance is less effective where the captured glass edge meets the supporting frame. This makes the type of framing system and the performance of that system critical when considering the energy performance of a building.
By upgrading the framing system of a building, as opposed to solely improving the glass, architects can in most cases dramatically improve the building’s thermal performance. While the up-front costs may
be slightly more than just using a thermally advanced glass, the framing system will reduce long-term costs significantly and ensure lasting performance over the life of the building.
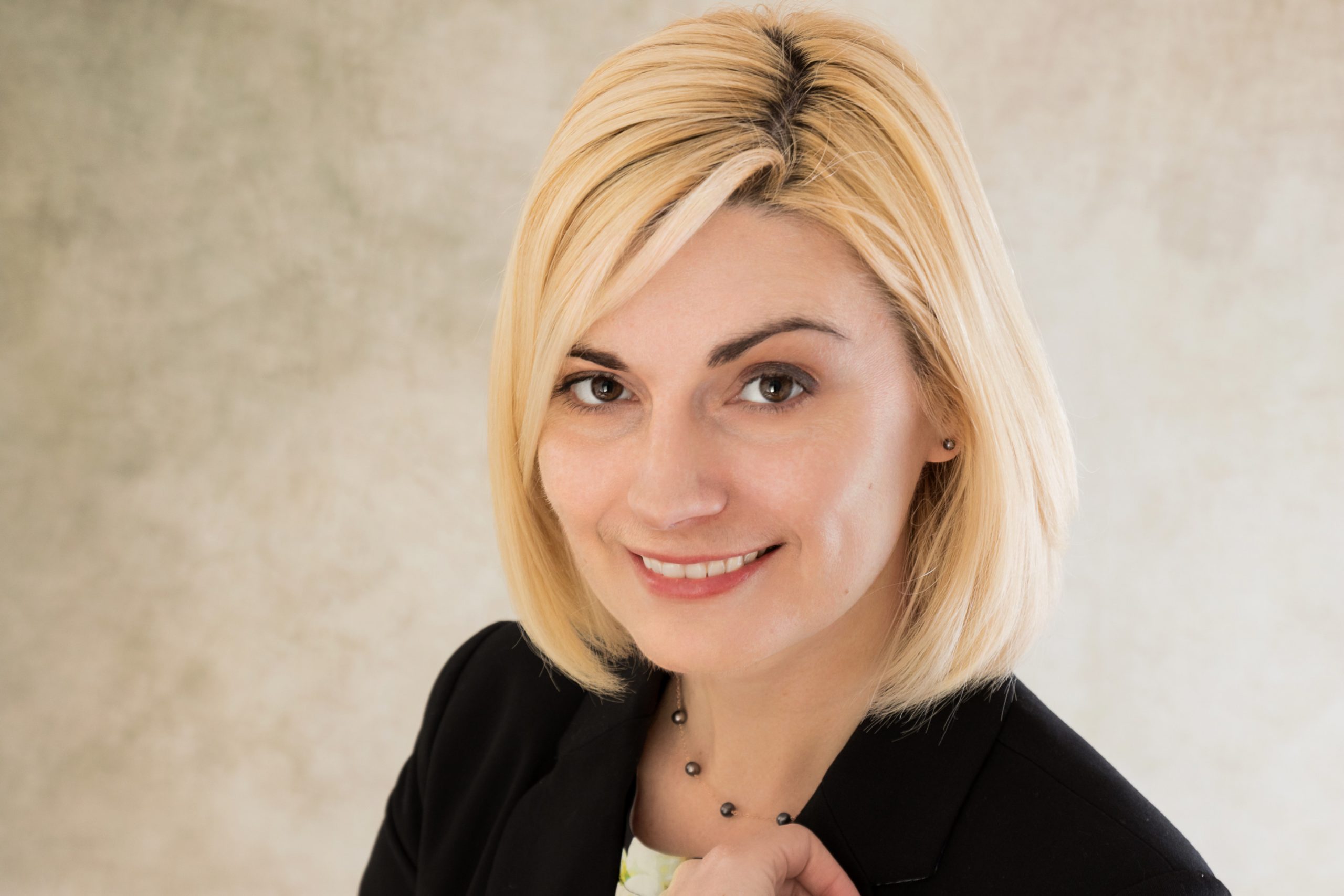
Annissa Flickinger
International Architectural Manager, Vitro Architectural Glass
We know the glass industry has done a very good job advancing glass performance. The bigger challenge is for curtain wall manufacturers, since the code’s requirements are for whole wall assembly performance, not just center-of-glass. Bigger thermal breaks, multiple airspaces, gas fill, and warm edge spacers are all tactics that can improve thermal performance.
For the past several years, I have been working with architects in overseas markets who need to meet the IECC requirements for glass performance. Depending on the climate zone, the solar performance or solar heat gain coefficient standards can be quite stringent. These requirements, as well as certain zonal ASHRAE requirements, have pushed glass manufacturers to develop new Low-E glasses.
Low-e coatings are a great example of nanotechnology being used to meet the IECC solar heat gain coefficient (SHGC) and U-value requirements. Quad-silver Low-E glass, which uses nanotechnology, can achieve an SHGC of less than 0.25 with a clear or low iron glass substrate. In the past, a tinted substrate was needed for this level of solar control. Now, quad silver Low-E glasses give architects a neutral-looking aesthetic while meeting IECC requirements.
We cannot be satisfied with the performance of Low-E glasses. Glass manufacturers need to be working on new products with lower SHGC and U-values.
In the meantime, architects are improving the performance of glass facades by adding elements such as vertical louvre shades or expanding rooflines to lessen solar penetration. Structures are also being designed in more unique shapes to create shaded courtyards and minimize direct solar energy.
It is exciting to work with architects on these challenging designs and finding the right glass solution that not only meets IECC requirements but satisfies the building’s programmatic needs. The 2018 IECC requirements may be more stringent, but it is the needed push to further advance Low-E glasses and push building design into more efficient geometries.
The post Architects and manufacturers discuss glazing and new code requirements appeared first on Facades+, Premier Conference on High-Performance Building Enclosures..